Los Sí y los No de Lean Six Sigma
- Francis López
- 29 abr 2021
- 15 Min. de lectura
Actualizado: 3 may 2021
Sinergia Empresarial - Lean Six Sigma
Las empresas inteligentes aprendieron que sus programas de mejora continua y del rendimiento operativo y, en especial, las iniciativas de calidad Lean Six Sigma, deben estar al servicio de un esfuerzo mayor: la gestión de procesos.

No hace mucho tiempo, "continuidad" y "estabilidad" eran las palabras más oídas en el área de operaciones de las empresas. Hoy, cuando tienen que enfrentarse a clientes creciéntemente exigentes y a una competencia feroz, la mejora del rendimiento operativo se ha convertido en un imperativo estratégico. En pos de esa meta, los ejecutivos siguen las rutas que indican "Centro de Servicios Compartido", "Implementación de ERP", "Cuadro de Mando Integral", "Cadena de Abastecimiento Integrada" y otra docena de programas, entre los que se cuenta uno de los favoritos en empresas altamente maduras: "Six Sigma" y "Lean".
Aunque cada una de esas iniciativas puede mejorar los resultados operativos, si el objetivo es que se integren con éxito deben colocarse bajo el paraguas de la gestión de procesos. De lo contrario, las empresas corren el riesgo de verse abrumadas por una multitud de esfuerzos desconectados. La proliferación de programas es peligrosa porque, mientras los empleados tratan de entender cómo se relacionan, reina la confusión y los recursos se diluyen. Además, alienta una competencia dañina entre los especialistas de cada sector de la compañía, que defienden sus respectivos programas y pretenden más recursos para implementarlos. También fomenta el cinismo; los empleados creen (con razón) que el equipo directivo no puede considerar seriamente tantos programas y, por lo tanto, piensan que ninguno se pondrá en práctica. Bombardier, Air Products and Chemicals, Johnson & Johnson y Merck, son algunas de las empresas que evitaron los peligros de la proliferación de programas, integrando sus iniciativas de mejora bajo el estandarte de la gestión de procesos. Al hacerlo, se aseguran de que esos esfuerzos se complementen, en lugar de competir entre sí, y pueden manejar todas las iniciativas en forma organizada. Cuando los programas de calidad Six Sigma también se ubican bajo el paraguas de la gestión de procesos, la empresa sacará provecho de esta importante herramienta, y evitará caer en la trampa de aplicarla donde no corresponde.
Todos juntos La gestión de procesos es un método estructurado para la mejora del rendimiento, que se concentra en el diseño disciplinado y la cuidadosa ejecución de todos los procesos de una empresa. Formalmente, un proceso de negocios es un grupo organizado de actividades que funcionan en conjunto, con la meta de crear valor para los clientes y satisfacer sus necesidades (por ejemplo, la ejecución de órdenes de compra, el desarrollo de productos y el soporte de post venta). A su vez, los empleados deben funcionar como un equipo, en lugar de concentrarse exclusivamente en sus tareas individuales y en proteger sus territorios. Finalmente, todas las actividades de un proceso de negocios deben estar guiadas por un diseño que indique cuáles deben hacerse, cuándo y por quién. Ese diseño es el que asegura repetición y coherencia.
Por lo general, las empresas pueden identificar entre cinco y 10 procesos de negocios importantes. El de ejecutar una orden de compra, por ejemplo, que involucra a todas las actividades de una compañía: desde el momento en que un cliente realiza el pedido, hasta que lo recibe y lo paga. Ese proceso trasciende las fronteras funcionales, e integra servicio al cliente, logística, finanzas y hasta fabricación, con el fin de satisfacer una meta común. Otros procesos, de nivel más alto, son igualmente englobadores.
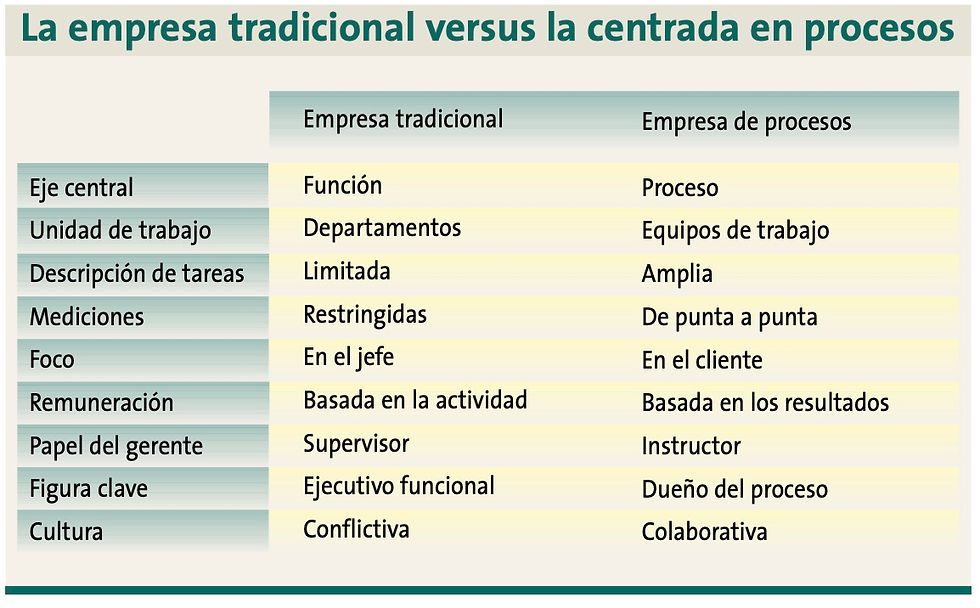
Aunque una empresa organizada por funciones lleva a cabo todas las actividades necesarias para convertir un pedido en dinero efectivo, no las encara como un proceso. Están a cargo de diversos departamentos que, habitualmente, persiguen objetivos de rendimiento diferentes. Debido a ello surgen conflictos, aumentan los costos fijos y el trabajo que no agrega valor. Además, como nadie es responsable de las actividades desde el inicio hasta el fin, tampoco hay nadie que establezca y haga cumplir un diseño general preciso y repetible. Las consecuencias obvias son la variación y la improvisación.
La gestión de procesos asegura que las actividades se piensen, diseñen y ejecuten en el marco de un proceso. Cuando los empleados reconocen que sus actividades individuales son parte de algo mayor, se alinean en torno de metas comunes. Cuando un proceso tiene un diseño explícito del principio al fin, la gente puede realizarlo de manera coherente, y los gerentes están en condiciones de mejorarlo en forma disciplinada. La gestión de procesos asegura que todos los procesos de una empresa estén bien diseñados, que los diseños se respeten y se mantengan actualizados.
La figura central de la gestión de procesos es el "dueño" del proceso, que debe ser un alto ejecutivo de la compañía. Esa persona tiene que lograr que los encargados de realizar el proceso lo entiendan, se capaciten, posean las herramientas necesarias y respeten el diseño especificado. También puede hacer cambios menores en el diseño, a fin de solucionar un defecto o para que aborde nuevas cuestiones. Si la brecha entre el rendimiento actual del proceso y el deseado es grande, el dueño de proceso debe liderar la iniciativa para crear un diseño del proceso completamente nuevo; es decir, un proceso de reingeniería.
Beneficios indudables Cuando se establece un riguroso diseño de cada proceso, el rendimiento aumenta porque no se malgastan recursos ni tiempo en esfuerzos inútiles, y los proyectos no caen en agujeros negros. A mediados del 2005, Caterpillar diseñó un proceso formal, de cuatro etapas, para concebir y lanzar nuevos modelos al mercado. Como resultado, el ciclo de desarrollo de nuevos productos disminuyó de ocho años a tres.
La gestión de procesos también aporta beneficios mediante la alineación en pos de una meta común, orientada al cliente. Es lo que hizo un fabricante de semiconductores a principios del 2010. Las órdenes de compra tardaban 180 días en ejecutarse porque la tarea estaba dispersa en múltiples departamentos y lugares, cada uno de ellos con metas de desempeño diferentes, pero ninguno con la responsabilidad total. Al fomentar una conciencia general del proceso completo, y establecer los tiempos y parámetros que todos debían cumplir, la empresa eliminó el "no es mi culpa", y el ciclo de cumplimiento de pedidos se redujo un 75 por ciento. La gestión de procesos también brinda un marco para la reingeniería: el rediseño deliberado y holístico del trabajo. El éxito de una empresa, en definitiva, depende de la ejecución eficaz de procesos bien diseñados.
Consideremos el salto que dio Progressive Casualty Insurance en el manejo de reclamos. Originalmente, una persona informaba un accidente de tránsito a un agente de seguros, quien le enviaba la información a un representante del servicio al cliente de Progressive. Este, a su vez, la enviaba a un gerente de siniestros. Luego de reunir varios reclamos del mismo territorio, el gerente asignaba al liquidador que se encargaría de inspeccionar el vehículo. Por lo general transcurrían entre siete y 10 días desde el momento del accidente hasta la visita del liquidador. Debido a que la rápida iniciación del trámite es un factor crítico para mantener satisfecho al cliente, Progressive resolvió mejorar el proceso. En 2012, al reconocer que no podía reducir el tiempo de espera exigiendo a sus empleados que trabajaran esforzadamente (ya lo estaban haciendo) o eliminando fallas en la ejecución (no las había), la compañía decidió rediseñar todo el proceso. Hoy, los liquidadores de Progressive están organizados en equipos. Un miembro de cada equipo se ocupa de recibir los llamados, y resuelve todo lo que puede por teléfono; si hace falta una inspección, se pone en contacto con alguno de los demás integrantes del equipo, que esperan en vehículos, y programa la visita. Ahora, el tiempo que transcurre entre el llamado y la inspección es de apenas algunas horas.
Los sistemas de gestión tradicionales son enemigos de los procesos, y fueron diseñados para compañías organizadas en funciones. Pero, a medida que la gestión de procesos empieza a arraigarse, todos los sistemas de la organización se re enfocan para dar soporte a los procesos. Los empleados trabajan en equipos, no en departamentos; su remuneración está vinculada a los resultados, no a las actividades que realizan ni a su antigüedad en la empresa; los gerentes, en lugar de supervisar, brindan asistencia a sus subordinados. Los sistemas de computación se integran para dar apoyo a los procesos en todas sus etapas, no a departamentos específicos, y la cultura alienta tanto la responsabilidad individual como la colectiva. Una empresa que ha institucionalizado la gestión de procesos y alineó los sistemas de gestión para darle soporte, es una empresa que está centrada en sus clientes y en sus procesos. (Ver cuadro "La empresa tradicional versus la centrada en procesos".)

Certifícate en Lean & Six Sigma
100% Español - incluye 100% términos en Inglés
Algo en común Además de conducir a un mejor rendimiento, la gestión de procesos aporta un marco para integrar iniciativas de mejora de rendimiento. Las más populares se basan en el despliegue de tecnología; otras en la instalación de nuevos sistemas de medición de desempeño, y algunas son de naturaleza más estratégica. Sin embargo, un cuidadoso análisis de cualquiera de ellas revela un tema común: los procesos de negocios.
Sistemas de Planificación de Recursos de la Empresa (ERP). En términos técnicos, un sistema ERP es una familia de módulos de software que comparten una misma base de datos. En la práctica, debido a que sus módulos están integrados, un sistema ERP se convierte en una herramienta para dar soporte a todos los procesos del negocio, desde el principio hasta el fin. La implementación de un sistema ERP pone en evidencia y transforma todos los procesos de una compañía. Cuando las empresas encaran esa iniciativa sin entender sus procesos, se exponen a un desastre. Al implementar un sistema ERP hay que pensar, primero, en la creación de nuevos diseños de procesos, y después en la instalación de un sistema de software que les dé soporte.
Integración de la cadena de abastecimiento. Una cadena de abastecimiento es, simplemente, un proceso de negocios que cruza las fronteras corporativas y funcionales. Abarca todas las actividades necesarias para crear y brindar resultados a los clientes de una empresa: las actividades a cargo de la empresa, de sus proveedores y de los proveedores de sus proveedores.
Integración de fusiones. Convertir a empresas independientes en una sola compañía es, de hecho, un ejercicio de estandarización de procesos de negocios. Los líderes de la compañía fusionada deben decidir qué procesos serán comunes en la nueva empresa, y cuáles pueden variar. También deben decidir si un proceso estandarizado tiene que basarse en un proceso existente o ser completamente nuevo.
Otras iniciativas. Las técnicas de Cuadro de Mando Integral (Balanced Scorecard) y de valor agregado económico (EVA) han desarrollado sistemas de medición que traducen objetivos corporativos en metas de rendimiento de procesos. La gestión de relaciones con el cliente (CRM) permite que todas las interacciones de un cliente con la empresa se manejen como un solo proceso. Y la lista sigue...

La lógica de six sigma El marco de la gestión de procesos es particularmente importante, cuando lo que despierta el interés de los gerentes es el más novedoso programa de mejora del rendimiento: "six sigma". Técnicamente, six sigma es una medida específica de calidad: 3,4 defectos por millón. La mayor parte de las empresas opera en un nivel de calidad mucho más bajo (por lo general, en el rango de 2 a 3 sigma; es decir, entre 66.000 y 300.000 defectos por millón). Pero, en realidad, la definición técnica es irrelevante: algunas compañías no necesitan alcanzar ese nivel; otras, en cambio, deben superarlo. En la práctica, six sigma se ha convertido en el nombre clave de un conjunto de metodologías y técnicas que se aplican para mejorar la calidad y reducir los costos. La metodología six sigma de uso más frecuente es conocida como DMAIC (sigla, en inglés, de definir, medir, analizar, mejorar y controlar), y lo que aporta es un método disciplinado para resolver problemas de negocios.
La premisa de six sigma es que las compañías deben tener altos niveles de calidad y bajos niveles de costos, y que un enfoque disciplinado erradicará los desperdicios y errores habituales en las operaciones. Six sigma no ataca el nivel superficial de los problemas, sino sus causas. Si los defectos son muchos, no los reduce inspeccionándolos y descartando los items defectuosos; por el contrario, mide y analiza cuidadosamente las operaciones, a fin de determinar con exactitud cómo y por qué se producen los defectos, y luego toma medidas para abordar esas causas.
Con DMAIC, la secuencia es la siguiente: se define y cuantifica un problema; se evalúa la información recogida para limitar y clarificar el problema; se despliegan las herramientas analíticas que permiten rastrear el problema hasta su raíz; se identifica e implementa la solución para esa causa básica; y, finalmente, las operaciones mejoradas se someten a un control continuo para impedir la recurrencia del problema. El equipo de herramientas de six sigma incluye una variedad de técnicas, principalmente de análisis estadístico de información y mejora de la calidad. Muchas de ellas se conocen desde la era de la gestión de calidad total (TQM); otras son más recientes y de mayor complejidad. Six sigma es una metodología basada en proyectos. Es decir, la unidad de actividad es un proyecto que aplica la metodología DMAIC para solucionar un problema de rendimiento específico. Los proyectos están a cargo de equipos, liderados por "black belts" (profesionales expertos). La norma es que un proyecto debe llevarse a cabo entre tres y seis meses, y generar ahorros de entre US$ 150.000 y US$ 300.000; un black belt debe liderar entre cuatro y seis proyectos por año. El poder de six sigma radica en la disciplina que aporta para manejar la complejidad de las operaciones de una empresa. Muchos factores pueden ser la causa de un problema de calidad: una máquina mal calibrada, materia prima que no cumple con las especificaciones, un operador que realiza una tarea de manera incorrecta. En lugar de buscar soluciones aleatorias, una empresa que emplea six sigma identifica la causa de un problema, y aplica sólo las soluciones apropiadas. Six sigma ha sido comparada con la tarea de un detective: para resolver un problema, filtra las pistas en forma lógica.
El proveedor erróneamente acusado. Una compañía farmacéutica experimentaba un rápido crecimiento en la demanda de uno de sus compuestos, pero la línea de producción del compuesto tenía un pobre rendimiento. La gente de la empresa pensaba que el problema residía en la mala calidad de la materia prima de un proveedor. Sin embargo, el análisis six sigma reveló el verdadero problema: variaciones de temperatura en diferentes partes de la planta de producción. Al ajustar el sistema de calefacción y ventilación para homogeneizar la temperatura, el rendimiento mejoró un 60 por ciento, y generó ahorros directos de más de US$ 17 millones. Paralelamente, el mayor rendimiento le permitió al fabricante posponer una inversión de US$ 500 millones para construir una planta adicional.
El caso del operador inexperto. Un fabricante de polímeros recibía quejas de sus clientes: aseguraban que el producto estaba contaminado. Las hipótesis sobre las causas eran varias. El análisis six sigma limitó el problema a los productos que se enviaban, en cajas, desde un depósito. Por alguna razón, esas cajas tenían agujeros en el fondo. Finalmente, se supo que al extraer las cajas de una pila para el despacho, inexpertos operadores del elevador de carga las perforaban. La solución fue simple: modificar los brazos del elevador que tomaban las cajas.
El misterio de la burbuja de aire. Como parte de su control de calidad, un fabricante de productos farmacéuticos tomaba, rutinariamente, muestras de sus tabletas, las disolvía en un líquido y luego hacía pruebas en la solución. Con frecuencia, los resultados de las pruebas eran distintos y demandaban altos índices de retrabajo. Six sigma encontró el problema en el paso en el que se agregaba aire al líquido, a fin de facilitar la disolución de las tabletas. Como no estaba especificado cuánto aire agregar, cada encargado de la prueba añadía cantidades diferentes. La solución consistió en establecer parámetros precisos de aireación, y cambiar de puesto a los empleados que no hicieran la tarea como se debía. El retrabajo se eliminó, la calidad mejoró y los costos se redujeron.
Limitaciones obvias Hasta las empresas que tuvieron éxito aprendieron que six sigma no sirve para todo. En ese sentido, las experiencias de Bombardier resultan instructivas. La corporación canadiense, que opera activamente en varios negocios —aeroespacial, transporte ferroviario, productos recreativos, servicios financieros—, en el 2000 tenía más de 80.000 empleados e ingresos por valor de 16.000 millones de dólares canadienses. Como su experiencia con TQM, a principios del año 2,000, había sido positiva, los líderes de la empresa decidieron, en 2006, involucrarse en una iniciativa de six sigma: entrenaron 200 black belts en la metodología DMAIC, y lanzaron más de 500 proyectos. Bombardier logró ahorros de 137 millones de dólares canadienses en flujo de caja durante cinco años, sobre una inversión en six sigma de 21 millones de la misma moneda.
En 2009, la empresa realizó una evaluación formal de sus esfuerzos de six sigma, y llegó a la conclusión de que, a pesar del éxito alcanzado, esos esfuerzos tuvieron serias limitaciones:
El foco de la mayoría de los proyectos six sigma fue limitado: sólo se concentraron en actividades menores y de pequeña escala, por lo general dentro de una unidad funcional de la organización. Cuando los gerentes intentaron aplicar la metodología a proyectos de gran escala, los resultados fueron insatisfactorios hasta que se redujo el alcance.
Six sigma no pudo alinearse con la estrategia general de la organización. Si bien cada proyecto individual resultó valioso, la suma de proyectos no hizo contribuciones a las principales metas de la compañía.
Los esfuerzos en six sigma no influyeron en las hipótesis básicas de la compañía ni en su estructura de organización funcional. Debido a que las mejoras sustanciales de rendimiento exigen un cambio fundamental, el impacto de six sigma fue limitado.
En otras palabras, aunque una iniciativa de six sigma basada en la metodología DMAIC puede conducir a una mayor calidad y a menores costos, no es eficaz para generar drásticas mejoras en el rendimiento del negocio. En la última década, empresas como IBM y America Financial redujeron sus costos en cientos de millones de dólares y, simultáneamente, la satisfacción de sus clientes aumentó, pero no gracias a DMAIC sino mediante programas de transformación previamente acordados. Los ejecutivos de Bombardier, así como los de American Express, Merck y Motorola, también llegaron a la conclusión de que DMAIC no fue un vehículo para la transformación de sus empresas.
Lo concreto es que las limitaciones de six sigma son inherentes a su naturaleza de régimen orientado a proyectos y a la solución de problemas. De hecho, utiliza herramientas de análisis estadístico para descubrir fallas en la ejecución de un proceso existente. Herramientas que no plantean interrogantes sobre una posible manera, completamente distinta, de ejecutar el proceso. Six sigma da por sentado que el diseño del proceso existente es correcto, y que sólo necesita ciertos ajustes para ser más eficiente. Ese supuesto no es el mejor camino hacia una mejora radical.
La orientación a proyectos de six sigma, que convierte a la metodología en manejable, simultáneamente limita su poder. Las empresas que la adoptan congregan a muchos equipos de trabajo independientes, que encaran problemas aislados. Es común que existan docenas, y hasta cientos de esos equipos, en operación. Organizarse en torno de un gran número de proyectos de pequeña escala supone una alta probabilidad de éxito y atractivos retornos sobre la inversión, pero no permite un ataque sistémico a los principales problemas de una compañía. ¿Cómo se relaciona six sigma con otras iniciativas de mejora del rendimiento? ¿Es autónomo, o encaja en un esquema general? Una vez más, se impone la gestión de procesos. La mejor forma de administrar una iniciativa de six sigma es considerarla un arma más del arsenal de la gestión de procesos.
Bajo el paraguas de la gestión de procesos Los procesos de negocios aportan el contexto para la metodología DMAIC. Antes de empezar un proyecto de six sigma, lo aconsejable es que la empresa cree un modelo de sus procesos, relacione el problema a solucionar con un proceso de negocios específico y trace un mapa de los pasos de ese proceso. El mapa del proceso brinda un marco analítico para identificar las acciones que originan el problema (por ejemplo, incorporar aire a un líquido o levantar cajas con un elevador de carga). Una vez identificada la causa del problema, el remedio (establecer especificaciones para la aireación o instalar brazos más cortos en el elevador) es directo y localizado en la actividad problemática.
Si bien DMAIC asegura la correcta ejecución de los pasos de un proceso y permite modificaciones menores en su diseño, cuando la brecha entre el rendimiento actual y el deseado es grande, ese proceso necesitará un diseño completamente nuevo. Y crear un diseño es algo que six sigma, por su orientación analítica antes que creativa, no puede hacer. Recordemos el caso de Progressive: no había una sola causa para que a la compañía le llevara 10 días el proceso de manejar reclamos. Por cierto, no había un "problema" en la ejecución de ese proceso; funcionaba correctamente. Pero necesitó un diseño nuevo cuando las circunstancias del mercado le exigieron responder a los reclamos en horas.
La diferencia entre mejorar el rendimiento del proceso y crear un nuevo diseño se relaciona con la diferencia entre desperdicio y trabajo que no agrega valor. El desperdicio proviene de actividades individuales errónea o incoherentemente realizadas; DMAIC es efectiva para rastrear las causas del desperdicio, a fin de que puedan eliminarse. El trabajo que no agrega valor, por su lado, es el que mantiene unido el proceso y, por lo tanto, no puede eliminarse rápidamente. El rediseño del proceso apunta a reducir la cantidad de trabajo que no agrega valor. Identificarlo es fácil; lo difícil es reorganizar el proceso para que la necesidad de ese tipo de trabajo sea menor.
Además, six sigma no puede alinear a los ejecutores de un proceso en torno de metas comunes. Con six sigma, los procesos de negocios sólo son el marco para un régimen de solución de problemas. Está ausente la noción de que constituyen el punto central de la organización de una empresa. Como descubrieron los ejecutivos de Bombardier en 2009, las ideas fundamentales de six sigma se manifestaban en las intervenciones de mejoras de rendimiento específicas, pero no en las operaciones cotidianas.
Six sigma no es un sistema de operación y de gestión. No transforma a una compañía en una empresa centrada en procesos. Tampoco aborda cambios de cultura, mediciones y recompensas, estructuras organizacionales ni otros sistemas de gestión necesarios para que los procesos se conviertan en el eje central de la organización.
Para superar las limitaciones de six sigma y sacarle el máximo provecho, las empresas deben ubicarla bajo el paraguas de la gestión de procesos. Entonces, cuando surge un problema y parece razonable una solución six sigma, el dueño del proceso la acordará con un equipo de proyecto, asegurándose de que esté en línea con las metas estratégicas de la empresa. (Ver cuadro "Los sí y los no de six sigma".)
Ese fue el enfoque que utilizó Bombardier. La compañía estableció un programa formal de gestión de procesos: identificó las metas de rendimiento de sus principales procesos, complementó DMAIC con una metodología para el rediseño holístico de procesos e instituyó un mecanismo para determinar si la situación requería un equipo de mejora de procesos o uno de rediseño. American Express, Merck y Motorola dieron pasos similares, a fin de que DMAIC quedara bajo el paraguas de la gestión de procesos.
Algunas compañías quieren ampliar la definición de six sigma, para que incluya la gestión y el rediseño de procesos. Pero hacerlo es como ampliar la definición de básquet para que incluya al béisbol. Six sigma debe ser parte de la gestión de procesos y no a la inversa. ◼︎
Por Michael Hammer

Commentaires